Cement Quality Control: How Manufacturers Ensure Strength and Durability
25.03.2025
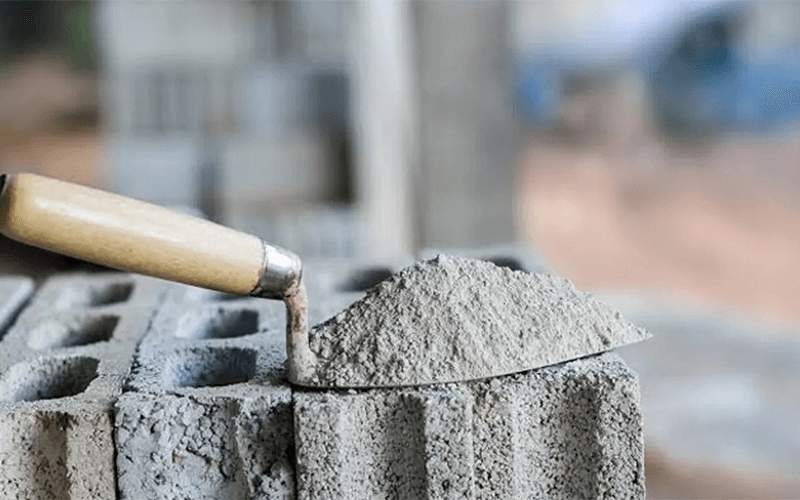
Introduction
Cement is the foundation of modern construction, making its quality a critical factor for structural strength and durability. To meet safety standards and customer expectations, manufacturers must implement stringent quality control procedures. This article explores how cement producers maintain consistency, identify flaws, and enhance performance throughout the production process.
Importance of Quality Control in Cement Manufacturing
1. Structural Safety and Reliability
High-quality cement ensures that concrete structures can bear loads and resist environmental stresses. Any compromise in quality can result in serious construction failures and increased repair costs.
2. Compliance with Industry Standards
Manufacturers must adhere to international standards such as ASTM, EN, and ISO to ensure product reliability. Compliance is essential for certification, legal requirements, and market trust.
3. Cost Efficiency
Defective batches can lead to construction delays, waste of materials, and higher operational costs. Rigorous quality control minimizes the risks of product rejection and project setbacks.
Stages of Quality Control in Cement Production
4. Raw Material Testing
The quality journey begins with sourcing raw materials like limestone, clay, and gypsum. These are tested for chemical composition, moisture content, and purity to ensure consistency in the final product.
5. Process Control in Kilns
During clinker production, precise temperature control and material feed rates are essential. Automation systems monitor kiln operations in real time to prevent defects and optimize energy usage.
6. Clinker Quality Analysis
Clinker, the intermediate product in cement making, is tested for mineralogy and reactivity. X-ray diffraction (XRD) and microscopy help evaluate its potential performance in cement.
7. Grinding and Fineness Testing
The final grinding stage impacts the surface area and reactivity of cement. Fineness is measured using Blaine air permeability or sieve analysis to ensure proper hydration and strength development.
Laboratory Testing for Strength and Performance
8. Compressive Strength Tests
One of the most critical quality indicators, compressive strength is tested at 3, 7, and 28 days. Standardized cubes or cylinders are subjected to crushing forces to measure performance.
9. Setting Time and Workability
Initial and final setting times are tested to ensure suitability for various construction applications. Workability is evaluated using the slump test, which reflects ease of mixing and placement.
10. Chemical and Physical Property Analysis
Cement is tested for key chemical properties such as SO3, alkalis, and free lime content. Physical properties like soundness, consistency, and heat of hydration are also evaluated in quality labs.
Advanced Technologies in Quality Assurance
11. X-Ray Fluorescence (XRF) Spectroscopy
XRF provides rapid and accurate chemical composition data for raw materials and cement. It enables real-time adjustments during production to maintain optimal quality.
12. Automated Sampling and Monitoring Systems
Automated systems reduce human error and provide continuous feedback on product parameters. These systems help maintain consistency and increase production efficiency.
13. AI and Machine Learning
Artificial intelligence is increasingly being used to predict quality outcomes and optimize formulations. Machine learning models analyze historical data to improve process control and reduce variability.
Packaging, Storage, and Delivery Quality Control
14. Moisture-Resistant Packaging
Cement is packed in moisture-proof bags or bulk containers to prevent degradation. Proper packaging extends shelf life and ensures product integrity upon delivery.
15. Storage and Transportation Checks
Manufacturers implement controls to prevent exposure to moisture and contamination during storage and transport. Regular inspections ensure that the product reaches construction sites in optimal condition.
Conclusion
Cement quality control is a comprehensive process that spans from raw material testing to delivery. With advanced testing methods and automation, manufacturers ensure their products meet the highest standards of strength and durability. As the construction industry evolves, cement quality will continue to be a cornerstone of safe and resilient infrastructure.